Wavelock Holdings are supported by TEAM Wavelock.
We confront work and explore the potential of people, technology and material.
This is an interview of the employees who will be creating the future in 2020.
Vol.1 Confronting challenging work alongside the historic Machine A. |
April 2020 |
---|
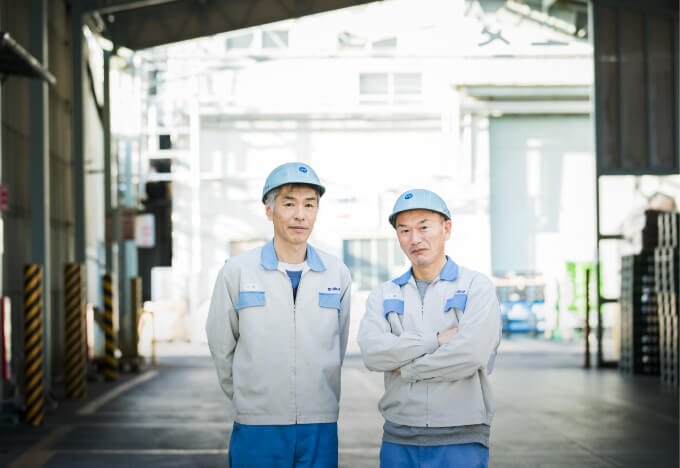
Material production is the core business of Wavelock Holdings. Innovex Co.,Ltd, Koga Plant located in Koga city, Ibaraki Prefecture is the main pillar of the production. Industrial Materials Production Department in Koga Plant, manufactures sheet and film by utilizing composite processing technology by laminating filament thread or base cloth with synthetic resin sheet. The processed product is utilized in construction sites, commercial facilities, medical facilities and agricultural sites. And in the Packaging department, they process polypropylene and polystyrene resin and create wide range of products such as food packaging materials and other packages.
Today, we saw a machine with M.F and N.E working at the Industrial Materials Production Department. They are experienced employees working 38 years and 37 years for our company.
“There are more senior people who have been working longer than us, so you should hear the stories from them….” The interview began with N. E’s modest words.
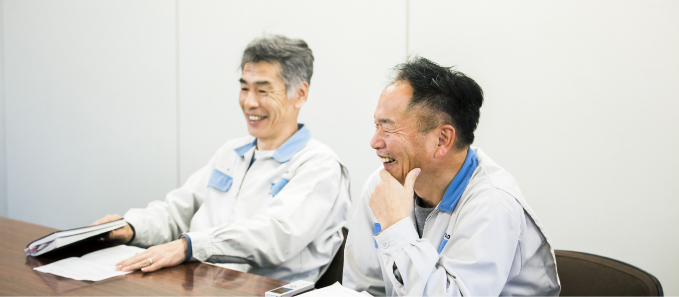
The name of the company Wavelock Holdings derives from the Wavelock production method. This method is to improve the physical strength of the sheet products by arranging multiple synthetic yarn in a wave between the plastic film and then locking them together to form a sandwich structure. During the establishment period, this technology was acquired from Bruno Romanin of TCM Italy and brought it back to Japan. Machine 1 in Koga Plant demonstrates the history to the present date.
−Was there Machine 1 since the beginning of the company?
M.F Yes, the former company was founded in 1964 and Machine 1 was brought in as the first machine. Former chairman brought back the machine and the technology from Italy.
−Is Machine 1 still in operation?
M.F Yes, it is still operating in full. We operate the machine 2 – 3 days per month.
−Tell us more about Machine 1 and the products that are being made at the plant.
N.E There are several machines for laminating. Machine 1 makes sheet for making rain ponchos and rain coats. Other machines make transparent sheet with yarn to make greenhouse or sheet to be made into vertical blind curtains used in the hospitals.
M.F The Melt Processing machine makes white sheet for covering the floor at the construction sites and sheet that is sound-proof.
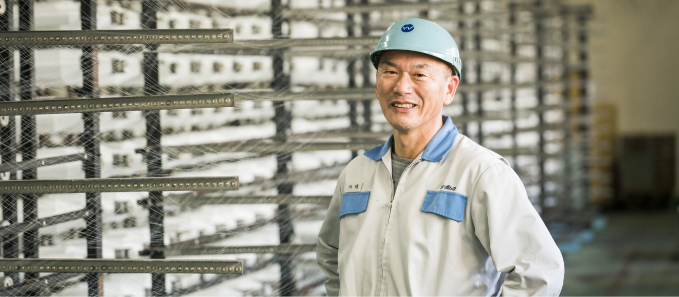
−M.F joined the company in 1982 and N.E joined in 1983. What was the atmosphere of the plant like then?
M.F We were all very young. The plant was also young. I think the average age of the employees were in their late 20s. You can just imagine, we were full of energy.
−What were you involved in at the beginning?
N.E I was assigned to the Melt Processing machine. It is a job where we make sheet for construction from the material. It took me 4-5 years to operate all the machines. This machine is operated in a team of 5 people. There are some experienced people and some beginners in the team so we rotate each position and learn each job. The final position you get to is called operation which is to manage the machine but it took a lot of work to get there.
M.F If you learn 1 of the 5 parts of the machine each year, you can become an operator in 5 years. But the operator is also a leader of the team, so it will not work if you do not have the skill to unite people. It requires some experience.
N.E. We were not casually learning the skill either. It is 30 – 35 years ago, so it was really hard work to memorize.
−It was like, “steal the job by watching”, right?
M.F Yes, that was certainly true. And there were senior people who were scary. (laugh)
N.E. We were strict about controlling the quality of the product while learning from strict seniors. It was hard work.
M.F. I also started my job at the same machine as Mr. N.E. Like him, I had senior people and soon had junior people as well. I was blessed with the human relationship.
−What was the challenging things?
M.F It was the operation work. I was surrounded by all the senior people and I had to manage the machine so it was nerve wracking but the senior people left the job to me. Also manufacturing products from materials was challenging. When we could manage to manufacture from resin compound to construction sheets, I was very proud of myself. I had to control the thickness of sheets, but at the beginning, it was very difficult. Later, when I could control and manage to make the right thickness at first go, I was so proud of myself.
−Do you think you were able to continue the job because it was rewarding?
N.E Yes, I think that’s why I was able to continue till now. And I was very fortunate with my seniors and juniors. They were tough but at the same time very caring. I think I was able to continue till now because of these relationships.
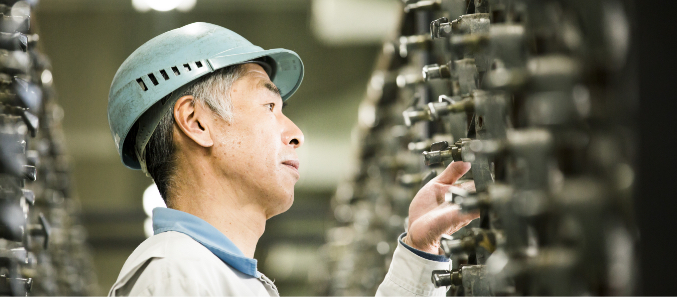
−What is the most important thing for you at work?
N.E Our former chairman often told us not to trouble other people. Work space is like living in a group. And while you are there, he used to tell us not to trouble people around you. For example, it is hard when there is an absence from work on the day while you are working in a team. I have been working for decades and I have tried not to do that. Even now I try to take this as a minimum manner.
M.F For me, it is how to handle reports and machines. I have tried to report bad news as soon as possible and not to lie about anything. And to treat the machine as if it is your child so it will not have malfunction or failure. It is hard to do it perfectly but continuity is power so I realize that I need to continue steadily.
−What is something that you are proud of about Koga Plant?
M.F. I am proud of the Machine 1 that you saw earlier, is still working actively. It has been working for over 50 years and the product is still in demand. I think that is something to be proud of.
N.E For me, it is also similar. I am proud that the machine that is over 50 years old is still moving with maintenance and with the support of the customers and hard work of the employees. It is not like the same product will come out once you switch the machine on. It is hard work. But I am proud that the machine is still very active.
−Tell us your goals for the future.
N.E Perhaps it is ordinary, but it is the development of Iwate. I want to educate the next leadership.
M.F I want to teach junior people. I do not have that much skill but I have a wish to educate the next generation. To be honest, I am happy when the young people do well at work. It is my small pleasure when I see someone who masters the job. I would like to increase that one by one. I would like to have the same attitude towards the customers and provide new products.
Machine can only be operated once there is a person. The skill to maintain the quality takes time, feeling with your hands and learning using your eyes and ears. At Koga Plant, the manufacturing skill of each person has been passed on to the next generation. The accumulation of these honest work is supporting our products and services.