Wavelock Holdings are supported by TEAM Wavelock.
We confront work and explore the potential of people, technology and material.
This is an interview of the employees who will be creating the future in 2020.
Vol. 5 Textile is a living thing. Believing in the sensibility of the anufacturer and pursuing the possibility of the woven mesh. |
Dec,2020 |
---|
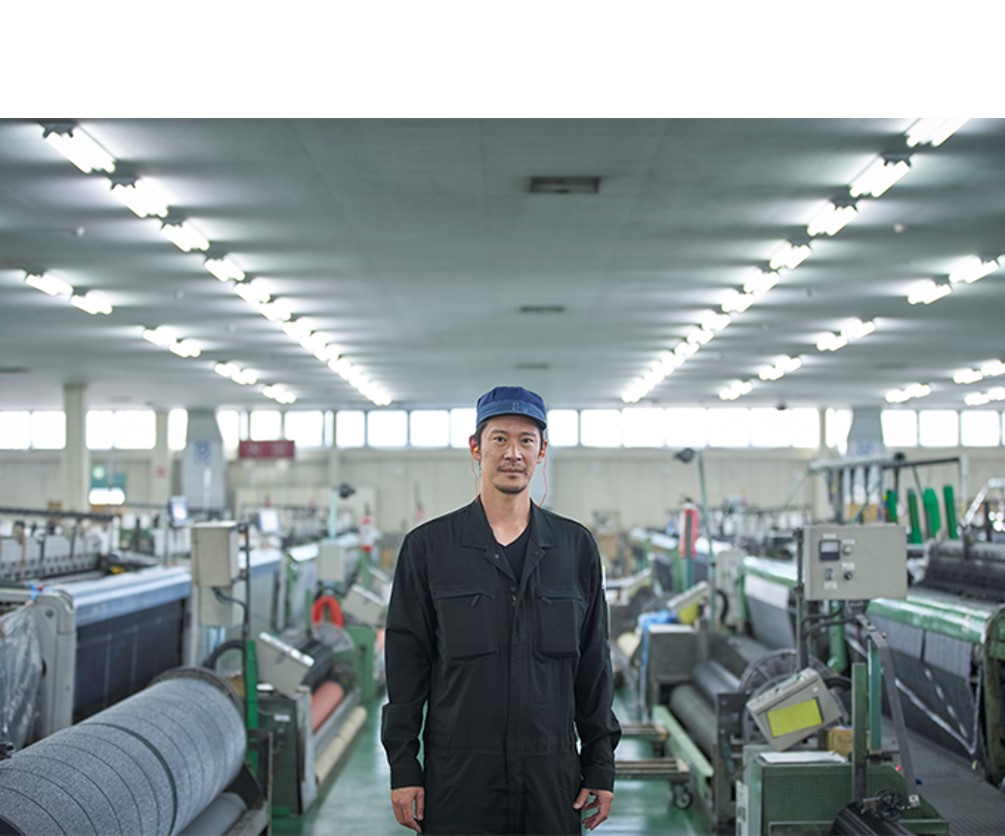
Innovex Co., Ltd Dio Fukuroi factory in Fukuroi city, Shizuoka Prefecture is located in the industrial area along the National Route 1. Inside the factory, we could hear the slashing sound from weaving machines alonng with a loud engine sound and creating fine woven mesh. Dio Fukuroi factory originally started as Tokai Cotton Cloth Co.,Ltd back in 1956 and manufactures the first insect repellent net using synthetic fiber in Japan. In 1964, Dio Fukuroi factory was established and changed its name to Dio Kasei. It became a part of Wavelock group in 2005 and in April 2020, it was integrated as Innovex Co., Ltd. To date, they have maintained the largest market share in Japan for manufacturing insect repellent net used for household screen doors. 30 people from the Weaving Division were working with the high-speed weaving machine. Today, we interviewed the manager, Mr Y.I. at the manufacturing site of Dio Fukuroi factory, and we touched upon the work style that values peoples’ sensibilities.

− How many people are working at the Dio Fukuroi factory?
Y.I At the moment, there are 86 people, 46 male and 40 female. There are also employees from our partner company and part time workers.
− Between the Dio Fukuroi factory and Dio Kakegawa factory, what are the departments divided into?
Y.I They both have Management department, Manufacture department and Logistics department and the Manufacture department is in charge of both factories. The Manufacture department at Fukuroi factory has established process in Weaving Division and Inspection Division . There is also a Spinning Division at Kakegawa factory and also another Division that are making other threads (Russel woven).
− What is the structure of Weaving Division?
Y.I There are 30 people working at the Weaving Division, approximately 60% men and 40% women. It is divided into 3 sections; creating warp, weaving fabric and maintenance. Creating warp is a process of preparing the warp thread (vertical thread) that was made in Kakegawa wrapped around the huge role called “ Beam”. Weaving fabric is a process using the machine and maintenance is to maintain the weaving machine. On weekdays, we monitor these process 24 hours a day.
* In the world of weaving, vertical thread is called a warp and horizontal thread is called a weft.
− There are people working night-shifts well as day-shifts, right?
Y.I Yes, that is true. I also worked both day-shifts and night-shifts for about 10 years. When I got used to it, I enjoued working for both shifts. You can spare more time for yourself. Currently, we are operating in 3 shifts.
− From the weaving machinery, how many varieties of products are being produced?
Y.I We have a lots of varieties. The majority is insect repellent mesh for household use and there are many variables such as different width and size of the weave (mesh). We also produce 20 to 25 variations of different sheets(or nets) for agricultural greenhouse.
− Does the insect repellent net contain repellent chemical?
Y.I It does not contain insect repellent chemical. It is called “insect repellent net” since it prevents the insects entering by the net. However, we do have a product called “Net that the insects dislike”. With this, we mix chemical into the thread but it is harmless to human and to the environment. It is very popular product since it prevents mosquitoes and moths from coming close.
− What kind of materials and forms are there for the insect repellent net?
Y.I For the insect repellent net, the majority is using polypropylene (PP) thread.
There are different kind of threads for different specifications.Different types of fineness of weave (mesh) is available; some are made in larger rough mesh and some are made in fine mesh. Regarding mesh units are counted by how many inserts have been made within 1 inch of lengths(2.54cm).
− What are the materials used for agricultural net?
Y.I For the agricultural net, we mainly use polyethylene (PE) and some we use polypropylene. We produce shading sheets for covering the greenhouse and black sheets used for covering the ridges of the rice paddy. But the form of the thread is very different from that of the insect repellent net. We use a flat shaped thread which we also call it a tape.
− How is the final product finished to be shipped?
Y.I It depends on customer by customer. For instance, insect repellent nets that are checked for inspection, it is cut into the length and packaged as final product. Also for agricultural materials, we adjust sizes to customer requirements.
One of our characteristics is that we do everything in-house from making raw material thread to the final product in Fukuroi and Kakegawa factories; so our strength is the speed of response by actually materializing product. Our environment allows us to make the thread to any product that are requested all on our own when our salesman inform us their needs for specific product.
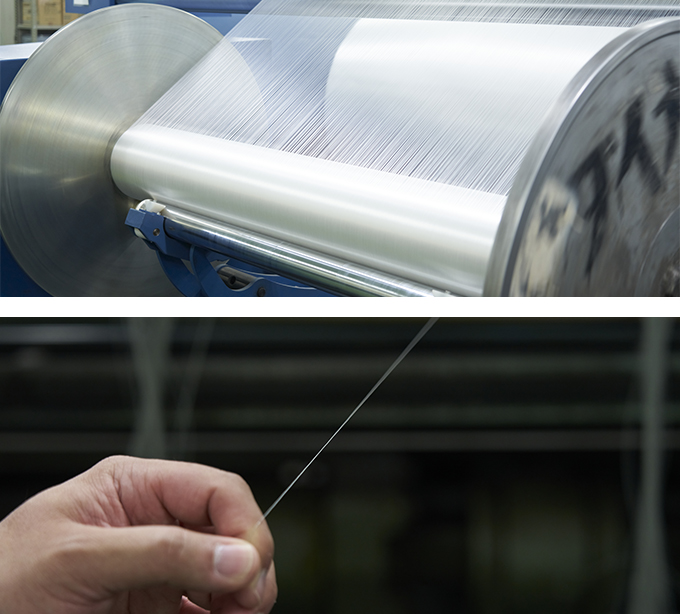
At the warp creating factory, they were working on preparing the warp. They wind the monofilament thread that was made in Kakegawa factory into a large roll called a beam while maintaining an even width. It is a spectacular site to see many weaving machines lined up at the weaving factory located right behind the wall. The weaving machine is operated at high speed while keeping a constant rhythm. Depending on the product, it spins 300 times per minute which means it is weaving 300 times per minute. During the interview, we were also able to talk to the factory manager; Mr. Y.S.
Y.S manager We have many types of weaving machines. Depending on how the weft (horizontal thread) is thread, it can be called water loom or air loom. This is a machine that throws the weft using the force of water or air. In our factory, we use a weaving machine called projectile weaving machine. The part called a projectile grabs the weft and flies at high speed, then it crosses the warp to weave.
The projectile weaving machine is very versatile and can handle thin yarn to heavy yarn which can create varieties of products. This is how we can develop new products according to the customer's reactions and market demands. It is easy to obtain a machine but the most difficult aspect is the technique how to adjust. The craftmanship of how to arrange it and how to adjust it depends on the skill of the responsible staff.
− I see that the weaving machine is very wide.
Y.I Yes, some machines has width that is over 4 meters. When we are weaving the insect repellant net which is 91cm wide, we can weave 4 nets at the same time. We can also adjust the size of the weave individually, so we can produce varieties of products.
− What are the most important and difficult parts of manufacturing?
Y.I The first thing we consider is the safety and that relates to the quality of the product. I try to communicate this to all the workers so that each person can raise their awareness.
The factory manager often says, “Textile is a living thing”. Even when we are using the same material to create insect repellent net, it comes out slightly different. It is really difficult to teach what quality is and though it may not sound good, there is a large part where you learn intuition through experience. The most difficult thing is to adjust the quality.
− Isn’t quality something you don’t notice if you are inexperienced?
Y.I Actually that is not true. When you are weaving, you naturally know when it is woven well and when it isn’t. We can see that in our process but people working at inspection have very sharp eyes since they are looking at several hundred meters of fabric every day. We sometimes receive severe criticism but we are grateful since they noticed what we missed.
− What makes the quality fluctuations?
Y.I There are several factors but for example, a slight difference in the tension can make the thread loose. Currently, we don’t have a lot of these cases as we have adapted necessary countermeasures and dealt with trouble shooting with the Spinning Division and Warp Creating Division.
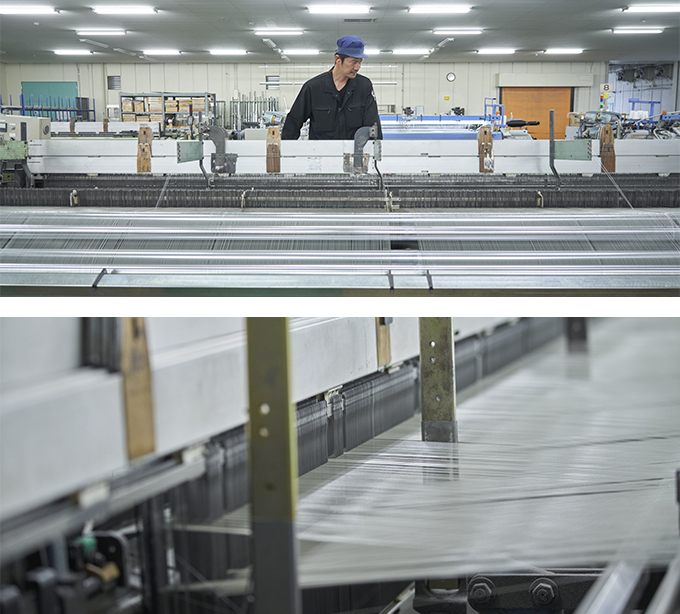
− How did you learn your work? How long did it take you to feel that you are accomplished?
Y.I When I joined the company, I learned from an experienced leader. He did not teach me all the details but it was like “learn by watching” while I followed him around. I don’t think I have accomplished yet. As I get older, I think I need to increase my capability, so I never felt I have reached accomplishment.
− Now that you are teaching others, what is your idea about conveying the message to the new people?
Y.I When I was learning, it was through my eyes, “learning by watching”, but now I am trying to adapt by adjusting myself at same level with each members, and then to teach the job from the beginning to the end. By doing this, I will know if they cannot do it, or they is not willing to do it, or they are not even thinking about it. When you teach how to cope the job, there are many people who will do it properly, so I am aware of these things. I try to convey even small details.
− What is your concern about how you face your job?
Y.I As I said earlier, "safety" is my concern. Not to get injured. Also think about others. Always work, considering the person who is in the next process. It is almost same as in “Service industry”. Not just thinking about your job but have a broader point of view. That is how I try to be.
− Do you have any products that you were involved with that you are attached to?
Y.I I am attached to all the new experiences. Even right now, I have just been promoted to become a manager since last April. To be honest, I am a bit worried if I can do all the work that I am responsible for. And also, there are many jobs that the members are helping too. They have started tackling it and are also worried if they can manage. I see them struggle, and see their suffering faces and I also feel the pain. But I am happy when I see a relief in their face when they say “ I managed to do it this way” once we got used to the job.
− Can you tell us your goal and things you want to work on in the future?
Y.I I have said this many times but since we are handling machines, "safety" is the most important thing. After establishing safe working environment, then to improve team work spirit, as well as improvement of quality of products, and lastly to focus on work efficiency. This is my goal to accomplish moving forward. I have another one. I really want to develop people who can think and work for others. I have always thought that it is important for each person to make no distinction between jobs and to be aware that even simple jobs are important for everyone. Even if there is job description, if you help others when you are free and work together, it will finish faster and at the end the good result will come out of it. I am trying to promote that kink of mentality throughout my department. I think everyone is changing gradually. They are all really good team members.
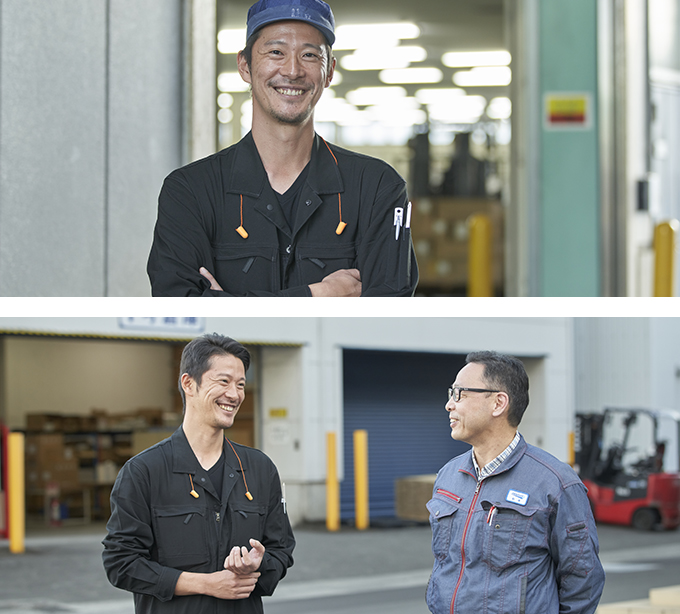